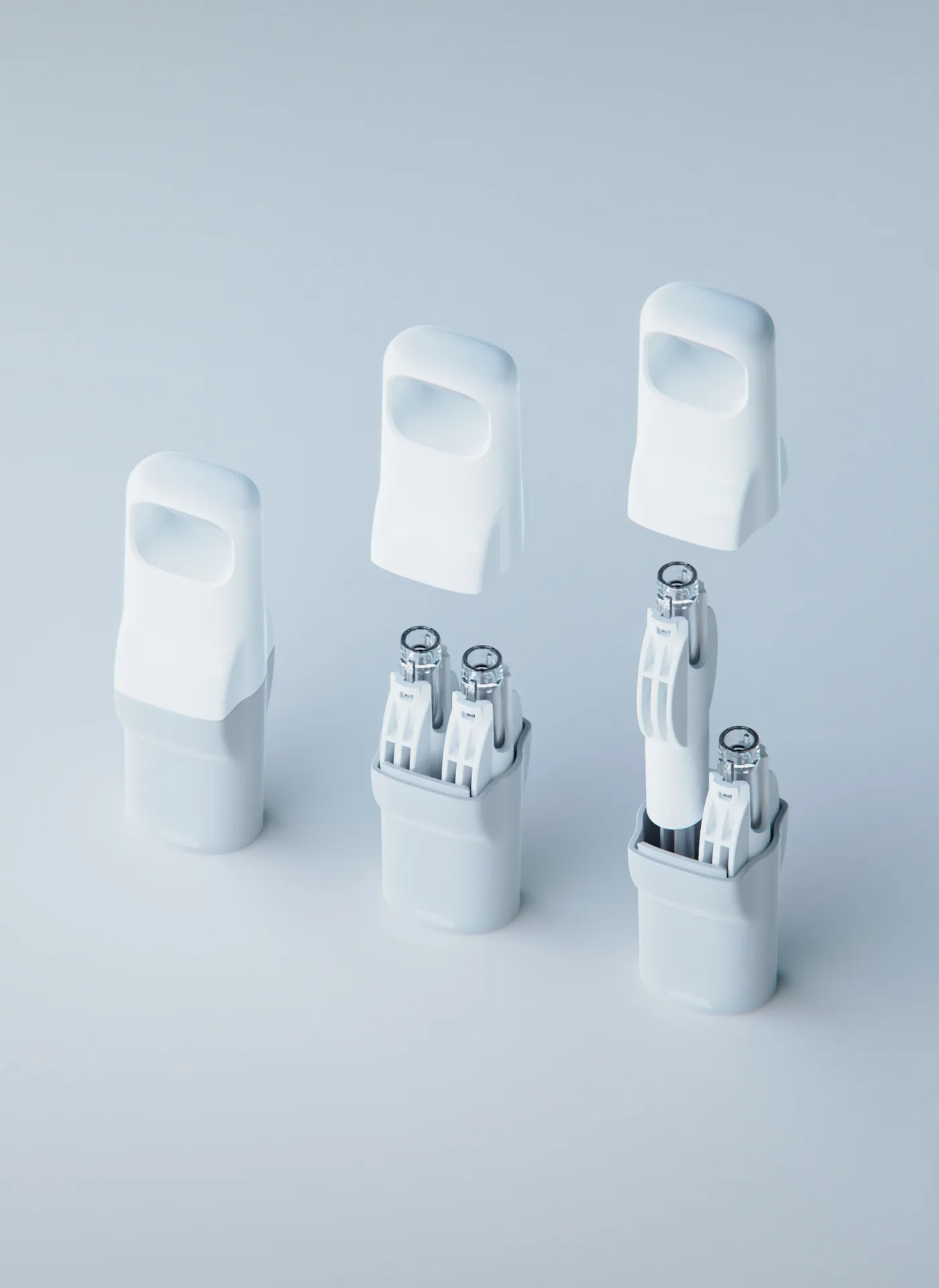
Scroll Down
デザイン Design
開発フェーズ 1
PHASE 0 - 1
- PHASE 2
- 基本設計
- PHASE 3
- 詳細設計
ユーザビリティ設計(デザイン)
機能 / 性能設計
信頼性設計
各種解析(CAE)
リスクアナリシス(DFMEA)
簡易製品試作(3Dプリンタ)
機能 / 性能評価
設計妥当性検証
製造パートナースクリーニング
製造パートナー選定
PHASE 4 - 6
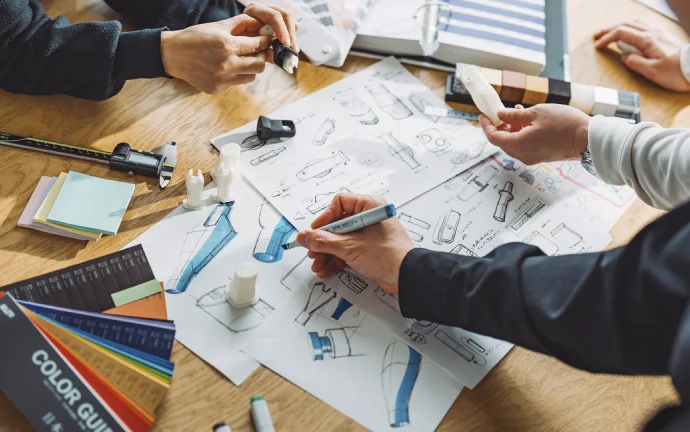
コンセプトの
実現と実証
整理された要件定義とコンセプトから、課題解決のアプローチを進めます。実践的な試作と検証のサイクルを回し、患者やユーザーにとってのポジティブな体験(PX、UX)を創り出します。
PHASE 2
基本設計
最先端のツールや技術を駆使して、デバイスのデザインと機構設計、解析、モデル化、分析、技術検証を行い、開発サイクル全体を通して、意思決定や設計の信頼性を高めます。
お客様と解決すべき課題の共有やコンセプトのアライメントを行い、完成品の輪郭をよりクリアにしていきます。
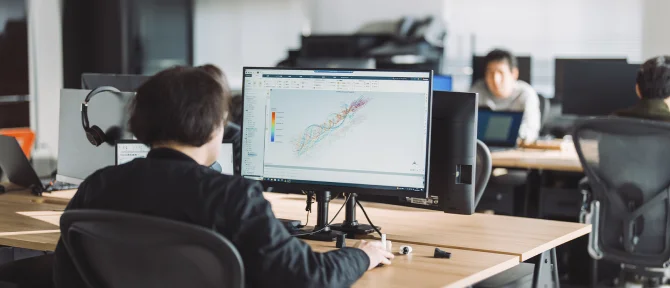
- ユーザビリティ設計
(デザイン) - 製品ビジュアルと使用感を統合させることで、コンセプトで据えた患者・ユーザー中心のユーザビリティを実用段階まで引き上げます。製品の『有効さ』『効率』『満足度』のバランスをデザインが監修します。
- 機能 / 性能設計
- コンセプトに対し、3Dプリント試作品による検証やCAEでのシミュレーションを活用し、仮説と検証を重ね、機能/性能の実現性を高めます。また、デザインとの密な連携で優れたユーザビリティ(UX)を作り上げます。
- 各種解析
(CAE) - 粉体や液体を扱う医療デバイス開発では、CAEの活用が欠かせません。流体解析用のAnsys Fluent、有限要素法解析用のAnsys Mechanical等を駆使して、臨床試験前の設計の信頼性を向上させています。
- リスクアナリシス
(DFMEA) - 製品開発の初期段階からリスクアナリシス(DFMEA)を実施することで、設計上のリスクを早期に特定して軽減することができます。これにより、将来的にコストのかかる変更を回避することができます。
- 簡易試作品
(3Dプリンタ) - “Fail Fast(早く失敗する)”を実現させる、3Dプリンタをはじめとする社内ラボの設備によって高速試作を行い、開発リードタイムを早めています。
- 製造パートナー
スクリーニング - 次フェーズでの量産製造パートナーを選定するため、製品や各種仕様、仕向けに適した複数の製造パートナーをリスト化。必要に応じて詳細プランを共有し、量産時に想定される課題まで抽出します。
PHASE 3
詳細設計
デバイス設計の最終フェーズです。DFMEAによって抽出された各種リスクの低減設計や、耐久 / 信頼性設計、生産性と製造プロセス設計を実施します。ここでは、最終製品と同等の仕様で試作金型を製作しての設計 verificationも行います。また、最終製品仕様に基づき、設備投資費を含めた量産にかかる概算費用を提示いたします。
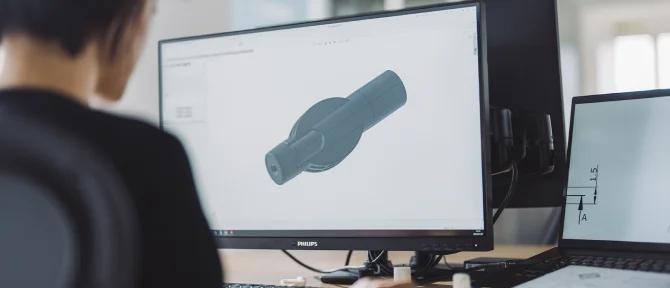
- 信頼性設計
- DFMEAによって抽出された各種リスクの低減設計や、耐久/信頼性設計、生産性と製造プロセス設計を実施します。
- 機能 / 性能評価
設計妥当性検証 - 信頼性設計と共に製造性考慮設計(DFM)を反映させ、試作金型を使った高品質な試作品で、デバイスの機能と性能を評価します。
- 製造パートナー選定
- スクリーニングされた各製造パートナーから、正式な量産製造先を選定します。最終製品仕様に基づき、設備投資費を含めた量産にかかる概算費用を提示いたします。
コラボレーション
医療・ヘルスケア分野で世界をリードする欧州や北米の先端技術を用いた課題解決をしています。
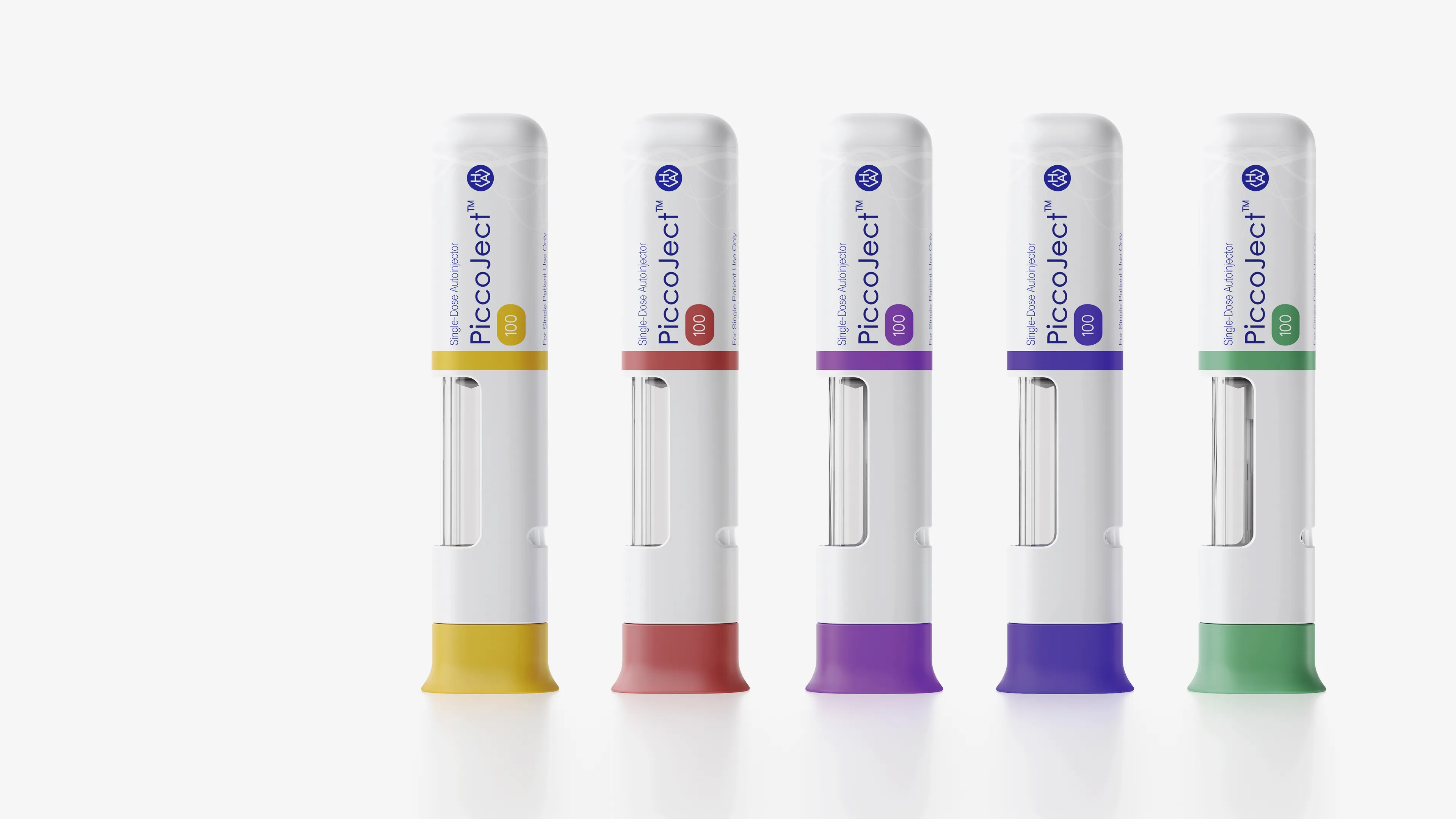